The Ultimate Guide to Molding Plastic Injection in Metal Fabrication
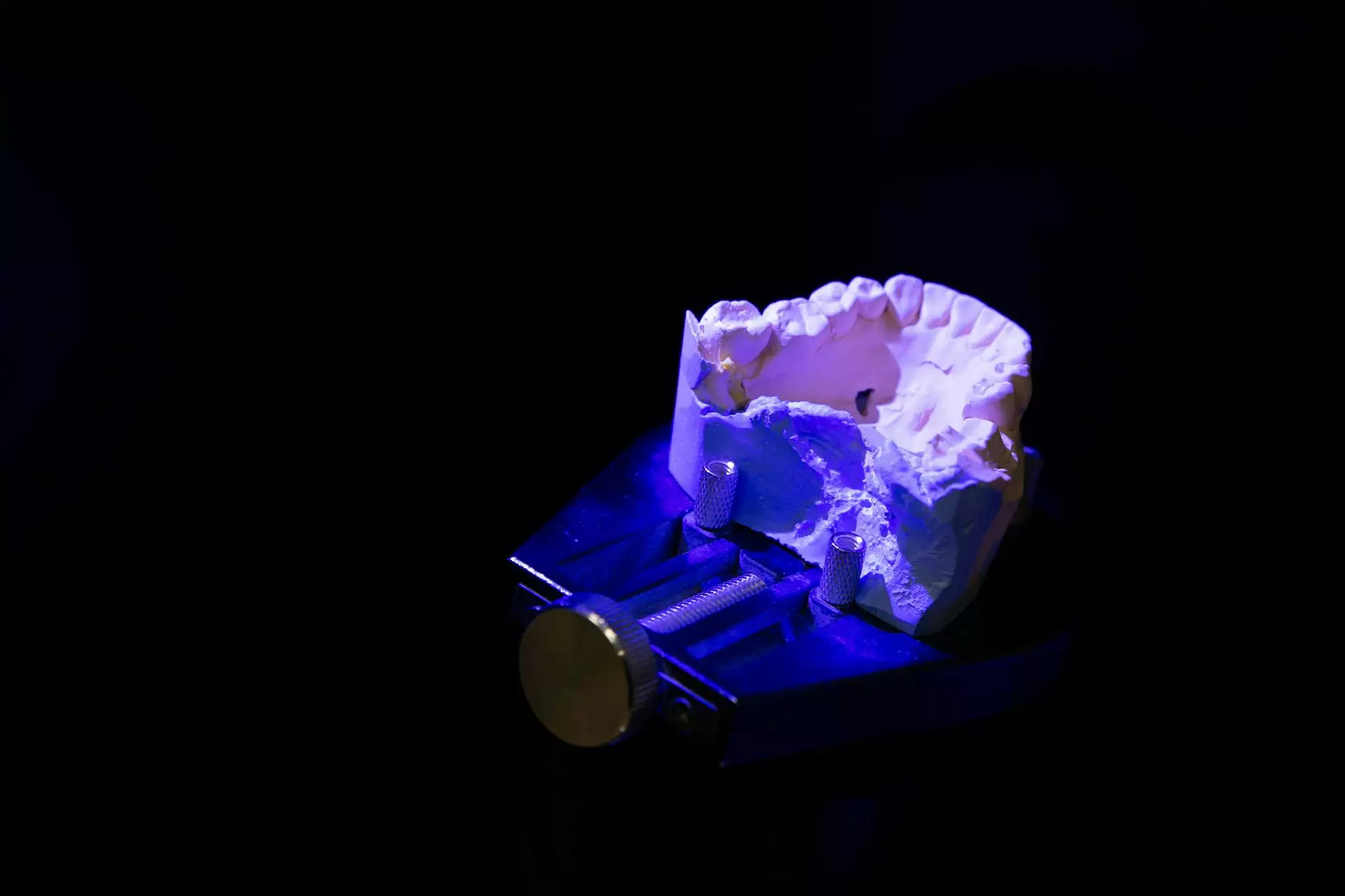
In the realm of manufacturing and metal fabrication, one innovative technique that stands out is molding plastic injection. This method harnesses the power of efficiency, precision, and versatility, enabling businesses to create complex shapes and structures from plastic materials. If you’re in the industry or looking to learn more about this process, you’ve come to the right place. This comprehensive guide will delve into the advantages, processes, and future trends of molding plastic injection.
What is Molding Plastic Injection?
Molding plastic injection is a manufacturing process that involves injecting molten plastic into a mold to create a specific shape. This method is widely used in various industries due to its capacity for high-volume production and the ability to produce intricate designs with high precision.
How Molding Plastic Injection Works
The process can be broken down into several key stages:
- Material Selection: The first step involves selecting the appropriate type of plastic. Different plastics have unique properties that make them suitable for various applications.
- Injection: The chosen plastic is heated until it melts and is then injected into a mold under high pressure. This phase is critical as it impacts the density and finish of the final product.
- Cooling: Once injected, the plastic cools and solidifies within the mold. This step is vital to ensuring the final product has the desired shape and strength.
- Removal: After cooling, the mold opens, and the newly formed plastic part is ejected. This step needs to be carefully managed to avoid any damage to the product.
Benefits of Molding Plastic Injection
Utilizing molding plastic injection brings numerous advantages, making it a preferred technique in various manufacturing sectors, especially in metal fabrication. Here are some of the most compelling benefits:
- High Efficiency: The process allows for rapid production cycles, significantly reducing the time to manufacture parts compared to other methods.
- Cost-Effectiveness: Although initial tooling can be expensive, the cost-per-part decreases significantly with higher production volumes, making it economical in the long run.
- Precision and Consistency: Molding provides high levels of accuracy, ensuring that each part meets stringent specifications with minimal variance.
- Design Flexibility: Designers can create complex shapes that may be impossible to achieve with other manufacturing processes, allowing for innovative product designs.
- Material Versatility: A wide range of materials can be used in injection molding, including thermoplastics and thermosetting plastics.
Applications of Molding Plastic Injection in Metal Fabrication
Molding plastic injection is not just limited to the creation of plastic parts; it plays a significant role in various facets of metal fabrication. Key applications include:
1. Component Production for Metal Parts
Plastic injection molded parts often serve as components for metal products, such as housings, fasteners, and brackets. These components can provide additional flexibility in design and can even act as insulating layers.
2. Tooling and Fixtures
Custom tooling and fixtures made through molding plastic injection can enhance the efficiency of metalworking operations, providing exact specifications for parts being fabricated.
3. Prototype Development
Before mass production of metal parts, businesses often utilize injection molding for rapid prototype development. This can save time and costs when assessing design feasibility prior to full-scale manufacturing.
Understanding the Metal Fabrication Stream
In the broader context of metal fabrication, it’s essential to understand how molding plastic injection fits into the operational flow. Metal fabrication includes processes such as welding, cutting, and assembling various metal structures. Molding plastic injection complements these processes by providing cost-effective and durable parts that enhance overall efficiency.
Integrating Injection Molding into the Fabrication Process
For companies looking to integrate molding plastic injection into their metal fabrication workflow, it’s important to consider the following:
- Collaboration with Design Teams: Close cooperation between design and engineering teams ensures that the molding considerations are accounted for during the initial design stages.
- Choosing the Right Materials: The choice of plastic material can affect the performance of the final product; therefore, an understanding of material properties is essential.
- Testing and Quality Assurance: Implementing a rigorous testing and quality assurance protocol will help maintain high standards across all manufactured components.
Trends in Molding Plastic Injection and Metal Fabrication
The landscape of manufacturing is continuously evolving. In the domain of molding plastic injection and metal fabrication, several trends are emerging:
1. Automation and Smart Manufacturing
With the rise of automation technologies, many companies are investing in smart machinery that facilitates faster and more efficient molding processes while reducing human error.
2. Sustainability Practices
More manufacturers are adopting sustainable practices by using recycled materials for molding and implementing methods that minimize waste during production.
3. Advancements in Material Science
Innovations in material science are introducing new plastics with enhanced properties, making injection molding a more versatile solution for various applications in metal fabrication.
Conclusion: The Future of Molding Plastic Injection in Metal Fabrication
As we look to the future, molding plastic injection stands at the forefront of manufacturing innovation within the metal fabrication sector. With its myriad benefits, from cost savings and efficiency to design flexibility and precision, businesses leveraging this methodology are likely to maintain competitive advantages in an increasingly challenging market.
By optimizing the integration of molding plastic injection into their operations, manufacturers can not only enhance their product offerings but also foster sustainability and adaptability in their business models. As new technologies and materials continue to emerge, the potential applications of this method will undoubtedly expand, solidifying its importance in the future of metal fabrication.
For more in-depth insights and tailored solutions regarding metal fabrication and molding plastic injection, reach out to professionals in the field such as Deep Mould at deepmould.net.